I’ll start off by saying that I bought something expensive, and now I need to justify it. Of course, “expensive” is a relative term, but we are a startup so we are cost-sensitive by necessity. This purchase was second-hand and a good deal, but much like my own personal splurges, I feel the need to justify the spending.
OK, it was an injection molding machine. No biggie. Like I said, at least it was a used model.
My first big lesson was that installation costs are not cheap. A 2007 machine may come at a discount, but facilities work in 2022 certainly did not. Then came the last-minute search to source anti-seize grease and drum of hydraulic oil as quickly as possible. I ran down the street to beg our automotive shop neighbors for anti-seize on a random Wednesday so that I wouldn’t waste the Engel technician’s time on site, and called everyone I could think of to buy a 55-gallon drum of oil ASAP because the pails I had wouldn’t be nearly enough to get the press started.
Step One: it turned on. A good sign, as I was worried that the battery would be dead. And it works! It successfully injects material into our test tools, although the temperature regulation of the tool could use some work.
I should back up a bit – before Step One came plenty of research, a test run at the vendor, and a tool build so that we would have a test tool and MUD base ready to go. But now that everything was delivered, installed, and passed the initial use test, I finally felt like I could breathe.
I’ve spent all my years since school in product development and manufacturing, so I feel fairly confident that developing our in-house molding capabilities is the right move for us if we continue down the path of molded, high grip parts and custom applications for B2B partners. We want to be able to prove out new concepts, test new materials, and make initial prototypes for customers. And this has to be better than the hand-actuated benchtop unit that we previously used to laboriously make thimble sized parts – a fun process that often caused our engineers to pull their hair out in frustration.
I also learned very quickly that designing parts for injection molding and designing molds are two very different beasts to tackle, and we do not have the benefit of expensive simulation software. Luckily, our product development engineer Pat was a quick study at 3D printed prototype molds, since that is our primary use of this “brand new” used Engel press at the moment. We may not have specific in-house injection mold design experts or even plastics processing engineers on staff, but we do have a wealth of knowledge, diverse backgrounds, and a lot of creativity and the ability to rapidly iterate. Now we do get fairly creative with our 3D printing and other prototyping methods, and the results can be surprising! Surprisingly good, surprisingly bad… it depends on the day.
So next question:
Can we form our fibers? So far – yes, although the flow length and part size factor in.
Can we sufficiently cool our fibers? Trickier, as we need to balance this with the heat required to fill the fibers. One of the issues with molding microstructures is striking a balance between fast injection, high resin temperatures, and cooling the parts before demolding to avoid deformation of the fibers.
Can we color mix adequately? For our purposes, yes.
Can I break a bolt and get a mold stuck? Definitely.
My next trial: overmolding
The main question I get a lot is this: can we use this machine to mold our silicone parts? Nope, sorry. An LSR press would be an entirely different investment and process.
This 50T press has proven to be a great tool for prototype ideation and evaluating those designs for manufacturability. It remains to be seen if I can get it to do everything that I want it to do without spending on additional auxiliary equipment, and the pressure remains to validate this purchase for small scale production for pilot launches.
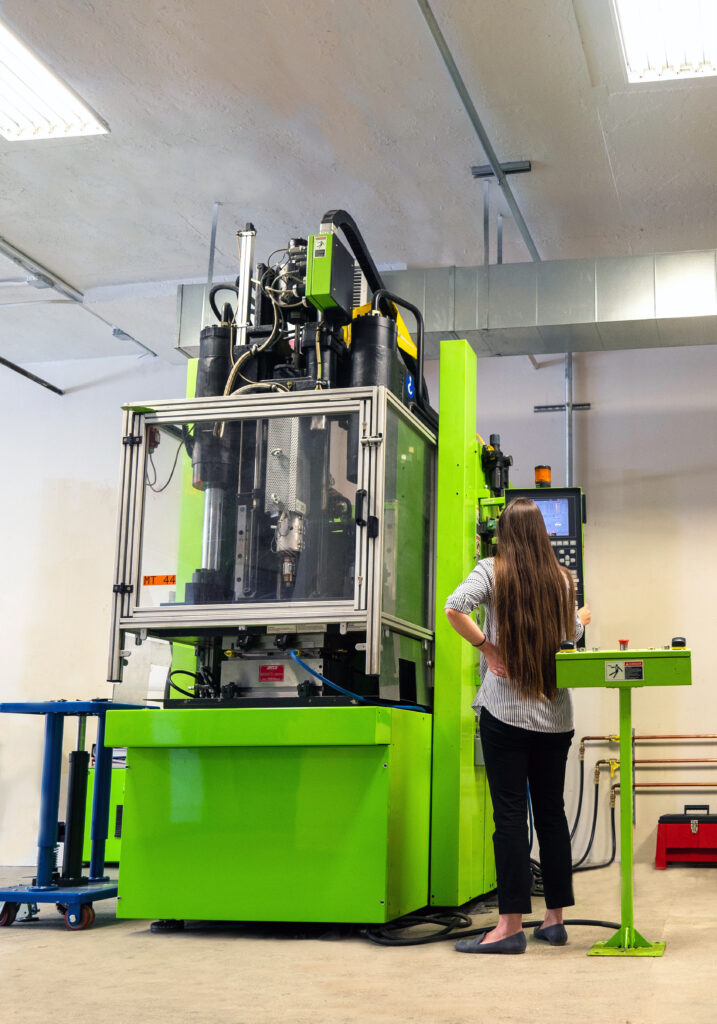